Die Story hinter unseren Metallic-Dekorfolien
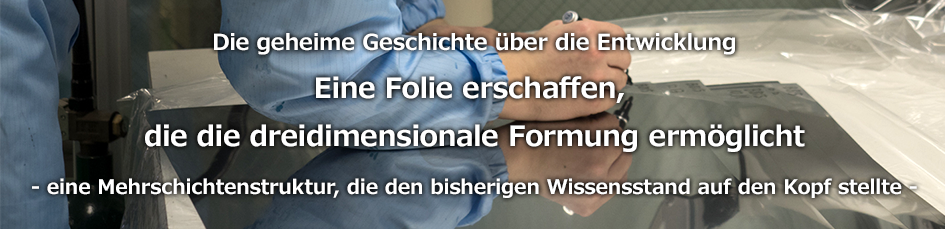
“Eine geschäftliche Anfrage aus den USA”
1998 erhielten wir eine Anfrage von einem Unternehmen in den USA, das Rückspiegelgehäuse in 3D-Form mit unserer Metallic-Folie entwickeln wollte. Genauer gesagt wollte das Unternehmen Dekorfolien ohne Verchromung herstellen. Japan Wavelock Co., Ltd. (heute Wavelock Advanced Technology) bot damals Dekorfolien für flache Oberflächen an, die für Türformteile/-verkleidungen und Stoßfängerformteile/-verkleidungen verwendet wurden. Das Unternehmen wollte den Metallglanzeffekt auch für Tiefziehteile (3D-Teile) verwenden.
Wir verfügten in unseren Produktgruppen über ein Produkt, das gebogen werden konnte, auch wenn es für falsche Dekorstreifen an der vorderen und hinteren Windschutzscheibe von Fahrzeugen entwickelt worden war. Wir waren überzeugt, dass wir die Anforderung erfüllen können, indem wir das Produkt an das Verarbeitungsverfahren des Kunden anpassen. Tatsächlich änderten wir die Kunstharze entsprechend dem neuen Verarbeitungsverfahren des Kunden und boten ihm so ein Prototyp-Produkt an. Laut Kunde eignete sich das Produkt gut für das Tiefziehverfahren, war aber ein wenig weißer als die Beschichtung. Es verlor sein metallisches Erscheinungsbild und die Oberflächenhärte war unzureichend. Kurz gesagt: Der Kunde war mit dem 3D-Verhalten zufrieden, jedoch blieben weiterhin diese 2 Probleme.
“Erzielen einer Metallic-Optik”
Auch wenn es sich um eine Flachfolie handelte, war die Optik nicht schlechter als die Qualität der Beschichtung, warum wurde die Folie weiß, wenn sie in 3D-Formen gebracht wurde?
Um das Problem zu verstehen und Korrekturmaßnahmen zu implementieren, begannen wir zunächst einige der alten Anlagen des Unternehmens instandzusetzen, um das Problem der Weißbildung der Folie zu reduzieren. Wir stellten die Bedingungen her, die es uns ermöglichen würden, eine Art Metallschicht zu entwickeln, die sich bei Tiefziehen in eine 3D-Form nicht verschlechtern würde. Nach wiederholtem systematischem Ausprobieren verschiedener Dünnfilmmetalle und zahlreichen Experimenten ermittelten wir eine bestimmte Metallart, die das metallische Erscheinungsbild beibehalten konnte, ohne weiß zu werden! Dies erforderte volle sechs Monate an Untersuchungen.
“Kompromiss zwischen Oberflächenhärte und Formbarkeit”
Wie können wir die Oberflächenhärte erhöhen?
Die Verwendung einer allgemeinen Hartbeschichtung führte zum Bruch, wenn die Folie zu einem 3D-Profil geformt wurde.
Wir suchten über mehrere Tage nach harten Materialien und brachten sie in 3D-Formen. Eines Tages konnten wir die gewünschte Härte und Formbarkeit an einem bestimmten Material bestätigen und trugen die metallisierte Schicht auf diese Folie auf. Dies löste das Problem, schuf jedoch ein neues. Die Materialkosten waren sehr hoch. Die Verarbeitungskosten erhöhten sich aufgrund der Dicke des Materials und entsprachen nicht mehr den Preisvorstellungen des Kunden.
“Die Herausforderung der Kostenreduzierung”
Welche Materialien können als dünne Folie geformt werden und sind für den Metalldünnfilm-Beschichtungsprozess dehnbar genug?
Wir setzten unsere materialwissenschaftlichen Untersuchungen fort und führten zahlreiche Versuch-und-Irrtum-Experimente durch. Schließlich entdeckten wir ein Dünnfilmmaterial, das tiefgezogen werden konnte und bereits für Getränkedosen genutzt wurde. Wir passten dieses Material an unseren Prozess an und erzielten eine erhebliche Reduzierung der Verarbeitungskosten bei der Beschichtung der dünnen Metallfolie. Da wir jedoch mit diesem Material nicht die gewünschte Oberflächenhärte erzielen konnten, entschlossen wir uns, zu einem zuvor gefundenen Kompromiss zwischen Härte und Formbarkeit zurückzukehren.
Auf dieser Weise entstand die „MTIA“-Konstruktionsfolie (eine metallische Zierfolie, die 3D-Formen ermöglicht), die aus einer mehrlagigen Struktur für den besten Ausgleich zwischen Oberflächenhärte und einer formbaren Metallschicht besteht.
“Einholung der Genehmigung durch den Vorstand”
Wir legten unsere Erkenntnisse dem Vorstand vor und erklärten, dass es sich bei der Neuentwicklung um eine mehrlagige Struktur handelt. Der Vorstandsvorsitzende lehnte die Probe mit der Begründung ab, „wenn wir zwei verschiedene Prozesse im Unternehmen anwenden, kann dies den Produktionsausstoß und die Qualität beeinflussen, sodass hieraus kein Vorteil für die Massenproduktion entsteht“.
Wir gaben jedoch nicht auf, sondern legten die Testkostenbilanz und die Berichte der wiederholten Prototypenfertigung vor und erklärten die Vorteile einschließlich der Möglichkeit, Farbvarianten herzustellen. Wir wiederholten diese Aktionen über fünf Monate, bis wir schließlich die Genehmigung des Vorstandsvorsitzenden erhielten. Zwei Jahre waren seit dem Beginn der Studien bis zum Erreichen dieser Stufe vergangen.
Tatsächliche Marktsituation”
Auch wenn wir das Produkt unserem Produktsortiment für das 3D-Formen hinzufügten, wurde damit in den ersten drei Jahren kein bemerkenswerter Umsatz erzielt. Viele Aufträge, die wir erhielten, waren punktuelle Aufträge für Touchpanel-Rahmen von Kühlschränken, Ersatzteile und Zubehör und ähnliche kleine Aufträge. Die Situation, in der wir das Produkt nur einmal pro Monat herstellten, hielt an.
“Der Wendepunkt”
Die Situation ändert sich dramatisch durch das Angebot, die Radmittelkappe durch ein Zierfolienteil zu ersetzen. Das Teil litt zu diesem Zeitpunkt unter Korrosionsproblemen, weil es verchromt war. Ein Kunde suchte nach einer Methode, um Korrosion vollständig zu vermeiden. Ein Produktionsprojekt war die natürliche Konsequenz. Da dies unser erstes Projekt zur Herstellung von Teilen für eine Automobilfertigungsstraße war, erforderte die Entwicklung umfangreiche Tests und Laborprüfungen.
Von der ersten Anfrage über die Erfüllung der Anforderungen des Endkunden bis zur Serienproduktion verging ein Jahr.
“Unser Ausgangspunkt war die Ersetzung der Beschichtung”
Derzeit arbeiten wir weiter an der Entwicklung neuer Produkte und der kontinuierlichen Verbesserung der Qualität unserer bestehenden Produktlinie. Darüber hinaus arbeiten wir mit Automobil-Designern an der Entwicklung neuer und farbiger Metallic-Designs mit intensiven Farbeffekten, die mit normaler Lackierung nicht möglich sind. Wir erkannten, dass wir Produkte mit Alleinstellungsmerkmalen, die Funktionalität und Nutzen bieten, und nicht einfach Ersatzprodukte für Beschichtungen oder Lackierungen anbieten mussten.
Da seit einigen Jahren verschiedene Industrieprodukte (wie Kraftfahrzeuge und Elektrohaushaltsgeräte) zunehmend mit Sensoren ausgestattet sind, wünschen sich unsere Kunden dekorative Materialien, die die elektromagnetischen Wellen einer bestimmten Wellenlänge nicht blockieren. Wir arbeiten intensiv und erfolgreich an der Entwicklung solcher Produkte.
Unser Ziel ist es, “unsere Kunden mit der besten Qualität und dem besten Aufstellung der Welt zu begeistern.
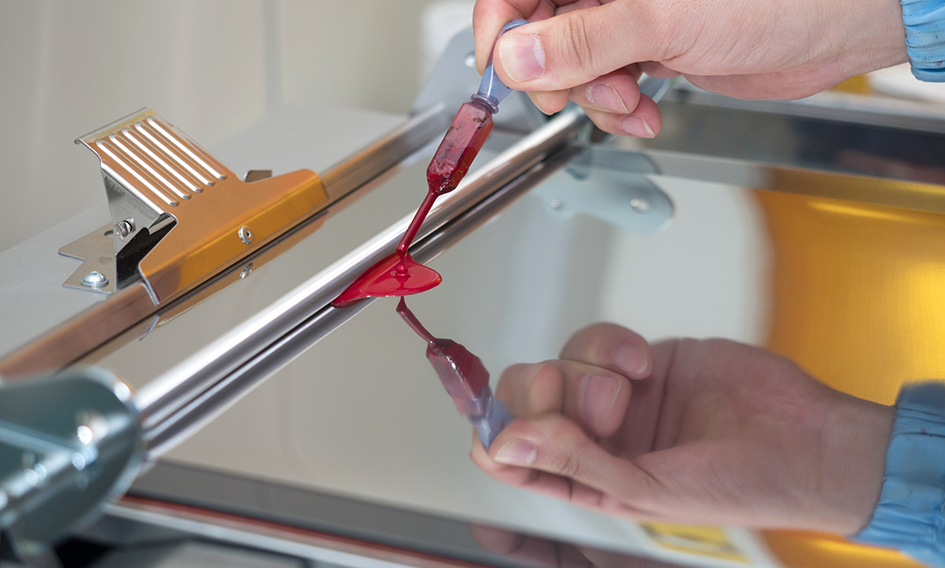
“Unsere Erfahrung mit Reisekoffern”
~Erlangung des Ausdrucks der Farbvariationen~.
Im Jahr 2000 schätzte der heimische Markt unsere Fähigkeit, hochwertige Aluminium-Attachékoffer in leichtem Kunststoff durch die Verwendung von dekorativen Metallfolien auszudrücken, und 2007 wandte sich ein heimischer Kunde an uns wegen eines metallischen Designs mit metallischer Haptik als Oberflächenmaterial für Reisekoffer. Durch die Verwendung einer Folie könnte die Gewichtsbeschränkung aufgehoben und das Metallic-Design zur Differenzierung des Produkts von anderen genutzt werden. Zum Zeitpunkt der Planung stand jedoch bereits fest, dass dieselbe Form in sechs Farben erhältlich sein würde, und das Projekt begann mit einem Versuch-und-Irrtum-Ansatz für Metallic- und Farbausdruck. Neben der Entwicklung des Verarbeitungsverfahrens und des Farbmaterials mussten auch alle Punkte der Produktprüfung geklärt werden, einschließlich der Stoßfestigkeit einer Tasche. Nach etwa einem Jahr Entwicklungszeit war ein Produktionssystem für die gesamte Farbpalette eingerichtet. Gleichzeitig konnte das Unternehmen die Technologie zur Steuerung von Metallic-Farben erwerben, die eine starke Waffe für die spätere Entwicklung von Automobilkomponenten darstellt.
“Wachstum durch Produkte mit Lichtdurchlässsigkeit”
~Verstärkung der Qualitätskontrolle~.
Als der Übergang von benzinbetriebenen zu Elektrofahrzeugen (EVs) ernsthaft begann, stieg die Zahl der Pläne für Fahrzeugteile mit LED-Hintergrundbeleuchtung. Diese Teile haben auf der Rückseite einen transparenten Kunststoff, und die LEDs werden von hinten beleuchtet, um tagsüber ein metallisches Design und nachts ein leuchtendes Design zu erzeugen. Obwohl kleine Teile mit einer farblosen und transparenten Rückseite erhältlich waren, wurden ab 2016 sogar Embleme auf der Fahrzeugaußenseite, die die Automobilhersteller symbolisieren, mit dem Konzept der Lichtdurchlässigkeit konzipiert. Diese Teile sind sozusagen das Gesicht eines Automobils und erforderten eine besonders strenge Kontrolle der Oberflächenqualität. Selbst kleinste Späne in den Metallschichten wurden bemerkt, und nach einer konzertierten Aktion des gesamten Werkspersonals zur Untersuchung der Ursache wurde festgestellt, dass beim Kontakt mit den spezifischen Führungsrollen ein leichter Abrieb vorhanden war. Nach Überprüfung und Maßnahmen zur Optimierung der Walzenoberfläche für den Substrattransport konnte das beanstandete Fehlen der feinen Metallschicht drastisch verbessert werden. Dieser Effekt wurde seitlich auf andere verwandte Geräte ausgedehnt, um die Wirksamkeit der Gegenmaßnahmen weiter zu festigen.
“Reaktion auf die sich ändernde Nachfrage nach Lichtdurchlässigkeit”
~Kontrolle der lichtdurchlässiger Farbe~.
Zu einer Zeit, als lichtdurchlässige Materialien immer mehr Anerkennung fanden, erhielten wir eine Anfrage eines Kunden zur Abstimmung der Farbe von lichtdurchlässigem Licht. Der Kunde wollte das Problem der Farbtonverschiebung durch die Farbe der Lichtquelle selbst lösen, wenn eine LED-Lichtquelle Licht durch eine Metallschicht aussendet. Als Antwort darauf wurde es notwendig, eine Methode zur Kontrolle der durchgelassenen Farbe zu entwickeln.
Nachdem wir alle durchgelassenen Farben jedes Grundmaterials bestimmt hatten, gelang es uns, die durchgelassenen Farben zu steuern, indem wir Farbkomponenten auf der Rückseite der Folie in der entgegengesetzten Richtung der Verschiebung entsprechend dem verschobenen Farbton anbrachten. Da die Verbesserung auf der Rückseite der Metallschicht vorgenommen wurde, war es möglich, die Transmissionsfarbe zu steuern, ohne das Metalldesign zu verändern, wenn die LED-Leuchten ausgeschaltet sind, und so die Anforderungen zu erfüllen.
“Bemühungen in Europa und neue Herausforderungen”
~Ausdruck der Funkwellen-Übertragungsleistung~.
Im Jahr 2019 erhielt unsere Tochtergesellschaft in Europa Anfragen zur Übertragungsleistung elektromagnetischer Wellen im Frequenzband der Millimeterwelle. Sie sagten: “Wir möchten einen Radarsensor anbringen, der den Abstand zwischen Fahrzeugen hinter einem vorderen Emblemteil erkennt. Herkömmliche Beschichtungen würden Millimeterwellen blockieren, können wir also nicht eine Folie verwenden? So lautete die Frage. Obwohl es möglich war, die Millimeterwellen-Durchlässigkeit von metallischen Dekorfolien in Abhängigkeit vom Zustand der Metallschicht zu beschreiben, gab es immer noch ein Problem bei der Umsetzung des Managements der Metallschicht, wenn man von der Nachbearbeitung der thermischen Verarbeitung der Folie ausgeht. Daher haben wir den Zustand der Metallatome und die Übertragungsleistung je nach Schichtdicke detailliert untersucht, um den Zustand der Metallschicht zu verstehen, der die Millimeterwellen-Transmissionsleistung stabil reproduzieren kann, und dies im Herstellungsprozess zu berücksichtigen. Darüber hinaus haben wir eine Methode zur Überprüfung der Leistung in Filmform entwickelt, die es ermöglicht, metallische Tonfilme bereitzustellen, die die Transmissionsleistung im Millimeterwellenbereich wiedergeben.
Im Jahr 2023 ist die Welt einem rasanten Wandel unterworfen, und auch das Umfeld der Automobilindustrie befindet sich in einem schwindelerregenden Wandel: der Aufstieg von CASE- (Connected, Automated, Sharing und Electrification) und MaaS-Geschäftsmodellen (Bereitstellung von Mobilitätsdiensten), die Verlagerung von Verbrennungsmotoren auf Elektro- und Brennstoffzellenfahrzeuge (FCV) und das wachsende Bewusstsein für Umwelt, Soziales und Unternehmensführung (ESG), das sich in erster Linie auf die Verringerung der Treibhausgasemissionen (THG) konzentriert. Angesichts dieser Trends suchen die Menschen auf der ganzen Welt nach dem besten Weg in die Zukunft. Wir werden mit größerer Geschwindigkeit, Flexibilität und einem Gefühl der Einheit als Team vorankommen als je zuvor.
- TOP
- Erforschung / Entwicklung
- Die Story hinter unseren Metallic-Dekorfolien